Home > Blog > "Breathability ≠ Permeability! Authoritative Evaluation Methodology for Fluid Permeability of Nonwov
-
Liu
Hi there! Welcome to my shop. Let me know if you have any questions.
Your message has exceeded the limit.
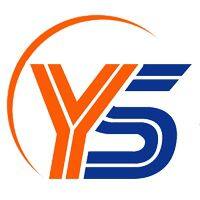
"Breathability ≠ Permeability! Authoritative Evaluation Methodology for Fluid Permeability of Nonwov
2025-07-16 09:11:49The opening: Lessons in blood and tears reveal the cognitive gap.
When a medical melt-blown fabric manufacturer faced a mass recall of surgical gowns due to excessive reliance on breathability data, revealing a harsh reality: gas permeability (breathability) and liquid barrier resistance (permeation) operate on entirely different principles. The mask stuffiness, diaper back-leakage, and filter oil leakage——90% failures all stem from misjudging "permeability". This article will demystify industry perceptions and use four testing keys to pinpoint the true penetration capabilities of nonwoven fabrics.
1、First battlefield: Conceptual clearing —— breathability = the essential divergence of penetration
Gas permeability and liquid permeability are like birds and fish – they must never be confused. Air permeability measures the ability of air to pass through (e.g., masks require ≥100 L/m²/s airflow), with the Fraser permeability meter as the core equipment. Permeability, on the other hand, evaluates liquid barrier efficiency (e.g., surgical gowns requiring blood penetration>60 minutes), relying on automated liquid permeability meters for precise detection. The most critical difference lies in their application media: the former targets free gas molecule diffusion, while the latter involves a life-and-death struggle between liquid surface tension and fiber infiltration. Take automotive filters as an example: measuring only permeability completely ignores the risk of high-viscosity engine oil penetration. ——When 0.3mm pores encounter 40℃ hot oil, the penetration rate can surge by 17 times!
2、The second battlefield: four test methods to overcome the actual difficulties
Liquid Penetration Sniper Test (ISO 9073-13) serves as the life-and-death test for medical protective equipment: A 0.1% sodium dodecyl sulfate solution (simulating body fluid surface tension) is dripped onto samples, with complete penetration time recorded. Medical-grade fabrics must exceed 60 minutes, while sanitary napkin surfaces require <3 seconds to prevent moisture. Air Penetration Blitz Test (GB/T 5453) reveals breathing resistance truths: Under a 100±10Pa pressure differential (simulating human breathing pressure), N95 melt-blown fabric must maintain ≤350Pa. A 5% pressure differential deviation triggers 35% data fluctuation! Virus-level Interception Test (ASTM F2298) employs laser particle counters scanning 0.1-10μm particles, requiring N95 masks to retain ≥95% of 0.3μm aerosols. Extreme Environment Dual-Test pushes materials to extremes: Oil permeability measured in-40°℃ cold chambers combined with 20Hz vibration tables simulating automotive filter conditions. Only data surviving rigorous torture can be trusted.
3、Third battlefield: a guide to the three invisible killers
The static voltage phenomenon acts like a stealthy threat in permeability testing, causing particle detection failure rates for 0.3μm particles to skyrocket by 58%——. Neutralizing ions with a 15-second ion wind rod proves crucial for breakthroughs. Temperature and humidity fluctuations are the primary nemesis of liquid permeability – only maintaining constant temperature and humidity at 23℃±1°C and 50% RH±5% can curb 35% data drift. For multi-layer composite structures like SMS non-woven fabrics, the dual-track approach of layered independent testing combined with holistic validation remains the only viable solution. A filter material manufacturer once faced millions of returned masks due to insufficient filtration efficiency caused by neglecting electrostatic interference – this starkly illustrates the critical gap between laboratory and real-world testing environments.
4、The fourth battlefield: life and death decision of equipment selection
Liquid permeability testers must be equipped with a six-channel automatic dropper arm (precision ±0.005ml) and millisecond-level infrared sensors. Manual dropper devices can cause 50% result distortion due to a mere 0.1ml liquid difference. Gas permeability testers need to cover the pressure differential range of 0-5000Pa and have built-in temperature/humidity compensation chips. Single-point sampling models will completely mask material uniformity defects. The more dangerous pitfall lies in test solution preparation: —— Using water instead of standard solutions to simulate bodily fluids is like using a wooden shield to block bullets – a protective suit manufacturer once paid millions in recall costs for this mistake.
Tags: Determining the permeability of non-woven fabrics